
Understanding Mouth Grinding Wheels
Mouth grinding wheels are an innovative tool that has taken various industries by storm due to their superior performance characteristics. These tools consist of abrasive particles bonded together to form a rigid circular shape that can efficiently grind or sharpen teeth-like structures known as claws.
The key features of mouth grinding wheels include robust construction using high-quality materials capable of achieving exceptional precision. Components like abrasion-resistant grains ensure durability and sustained sharpness over extended periods.
Comparison with Traditional Grinding Wheels
The primary difference between traditional grinding wheels and mouth grinding wheels lies in their design and functionality. While traditional grinding wheels serve a broader range of applications, mouth grinding wheels are specifically designed for tasks requiring intricate detailing and fine finishing.
Advantages of mouth grinding wheels include enhanced stability during operation, reduced heat generation, and improved waste management given their targeted application scope. The ability to conserve material while maintaining high precision makes them an attractive alternative to conventional options.
Benefits of Using Mouth Grinding Wheels
Enhanced Precision and Quality
Mouth grinding wheels excel in delivering remarkable accuracy, leading to significant improvements in the quality of finely-processed products. Their meticulous finish ensures fewer errors and higher conformity to desired specifications, thus producing consistently excellent outputs.
For example, when applied in the automotive sector, these tools facilitate manufacturing parts that exhibit micro-level precision, vital for operational integrity and safety.
Increased Production Speed
Another substantial benefit is the acceleration of production timelines without compromising quality. With optimized efficiency, businesses can expect faster turnaround times—a critical factor in competitive markets.
Case studies have demonstrated time savings upwards of 30%, transforming batch production logistics into seamless operations. This can mean more projects completed within shorter periods, ultimately enhancing profitability.
Cost Efficiency
Using mouth grinding wheels translates to cost savings in several ways. Over long-term use, firms will find reductions in operational costs attributed to decreased material waste and lower energy consumption rates.
Furthermore, replacing traditional grinders with mouth grinding wheels can minimize downtime owing to maintenance needs, thereby contributing to consistent production continuity.
Integration Strategies for Seamless Workflow
Assessment of Current Production Processes
Before integrating mouth grinding wheels, a thorough evaluation of existing workflows is crucial. Identifying compatibility issues and areas needing improvement forms the basis of a strategic implementation plan.
Step-by-Step Implementation Plan
- Initial Setup and Calibration: Begin by properly setting up and calibrating the new equipment based on manufacturer guidelines.
- Training Staff: Provide comprehensive training to employees for effective operation and maintenance of mouth grinding wheels.
- Continuous Monitoring: Implement a mechanism for monitoring ongoing uses and making necessary adjustments for optimal performance.
Maintenance and Care
Regular Maintenance Practices
A proactive approach towards regular upkeep encompasses daily cleaning routines, weekly inspections, and monthly calibrations. Required tools may include soft brushes, specialized cleaners, and checklists to ensure all practices adhere to standards.
Troubleshooting Common Issues
Common problems such as uneven wear or unusual noise should be addressed promptly to avoid exacerbation. Solutions might involve realignment procedures or part replacements, with professional repair services on standby for critical repairs.
Real-World Applications and Success Stories
Industry-Specific Examples
Mouth grinding wheels have revolutionized multiple sectors including automotive manufacturing, where they enhance the precision crafting of engine components. In aerospace engineering, their adoption enables the creation of highly detailed parts essential for flight mechanics.
Testimonials and Case Studies
Companies across various industries have reported measurable benefits post-adoption. For instance, one automotive manufacturer noted a 15% increase in product reliability coupled with a 20% reduction in production cycle times.
Future Trends and Innovations
Technological advancements promise further enhancement of mouth grinding wheels' capabilities. Emerging innovations focus on incorporating AI-driven precision adjustments and eco-friendly materials, heralding a promising future.
Sustainability Considerations
An emphasis on sustainable manufacturing methods underscores the transition towards greener practices. Utilizing eco-friendly abrasives and processes significantly bolsters environmental conservation efforts.
Tips for Maximizing Efficiency
Best Practices for Optimal Performance
Consistent performance relies on techniques such as proper storage conditions and gentle handling to elongate tool lifespan. Detailed logs documenting usage patterns can also aid in foreseeing required interventions.
Expert Recommendations
Insights from experts suggest continuous learning through resources like technical books, online courses, and participation in industry webinars for broadening knowledge about advanced grinding technologies.
Visual Aids and Demonstrations
Instructional videos offering step-by-step guides along with visual demonstrations provide practical insights into effectively utilizing mouth grinding wheels.
Additionally, infographics and diagrams clearly illustrate comparative advantages and streamlined operational protocols, ensuring organizations can quickly reference best practices.
Final Thoughts and Next Steps
Actionable Steps for Immediate Implementation
A quick-start guide listing immediate actionable steps helps teams swiftly adopt new practices. Items such as setting clear objectives, assigning responsibilities, and using progress tracking mechanisms can streamline integration.
Encouragement to Innovate and Adapt
To stay ahead, companies must embrace continuous improvement and adapt to rapidly evolving industry standards. Remaining informed about the latest trends and employing ongoing strategies for process optimization fosters sustained success.
Additional Resources
Further Reading and Research
Expand your understanding with recommended literature covering advanced grinding wheel technologies. Numerous articles, papers, and books are available for deeper exploration.
Supplier and Manufacturer Information
Reliable suppliers like SUNNY MACHINE offer high-quality products and expert consultations for tailored solutions. Contact these professionals to obtain customized advice suited to specific production needs.
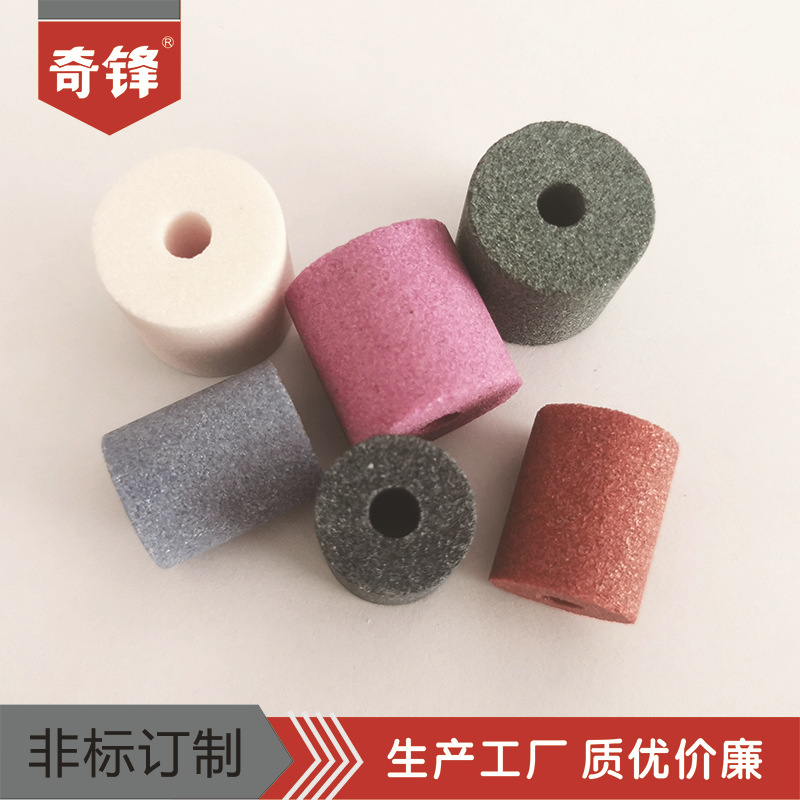