
The Significance of Claw Grinding Wheels
In various industrial applications, claw grinding wheels play an essential role by offering efficient material removal and precision shaping. High-quality grinding wheels affect productivity and product quality significantly, making them vital to sectors such as automotive, aerospace, manufacturing, and maintenance services.
Importance in Industrial Applications
From cutting hardened steel to shaping softer materials like aluminum, claw grinding wheels provide unmatched versatility. Their usage spans across multiple processes including deburring, surface finishing, tool sharpening, and more. The well-engineered design ensures minimal downtime and extended tool life, enhancing overall operational efficiency.
Varieties of Claw Grinding Wheels: 20 Claw vs. 25 Claw
The primary differentiation between the two main types—20 claw and 25 claw grinding wheels—lies in their number of claws. This distinction impacts their specific use cases; for example, 20-claw grinding wheels are often chosen for coarser tasks requiring rapid material removal. Conversely, 25-claw variants offer finer granularity, making them ideal for detailed work and achieving smoother finishes.
Selection of Raw Materials
Types of Abrasives Used
Choosing the right abrasives is crucial for ensuring performance and durability. Two commonly used abrasives are:
- Aluminum Oxide: Known for its toughness and strength, Aluminum Oxide is perfect for high-speed operations.
- Silicon Carbide: Offers superior hardness and thermal conductivity, making it suitable for hard metals and non-metallic substances.
Binding Materials: Resin or Vitrified Bonds
The binding agents hold the abrasive grains together, affecting the wheel's overall resilience and application range. Resin bonds provide flexibility and shock resistance, while vitrified bonds ensure rigidity and maintain structural integrity under high pressure.
Quality Control Measures in Raw Material Selection
A rigorous selection process ensures that only top-tier raw materials are utilized. Quality checks involve assessing grain size, purity, and consistency, which collectively enhance the wheel’s longevity and effectiveness.
Formulation and Mixing
Precise Ratio of Abrasives and Binders
A meticulously calculated ratio of abrasives to binders forms the backbone of any effective grinding wheel. This balance directly influences traits like sharpness, wear rate, and heat dissipation capabilities.
Mixing Techniques for Uniform Distribution
Uniform distribution of these components is achieved through advanced mixing techniques. Methods vary but generally incorporate both mechanical and manual stirring mechanisms to guarantee homogeneity throughout the mixture.
Impact on Performance and Durability
The formulations' accuracy has a direct bearing on the wheel’s performance and lifespan. A well-mixed formulation results in fewer defects, consistent cutting action, and enhanced user safety during operation.
Molding and Shaping
Molding Methods for 20 and 25 Claw Designs
- Compression Molding: Ideal for creating denser structures, this method involves applying pressure to shape the material within molds.
- Injection Molding: Utilizes injected molten material into pre-designed molds, enabling complex shapes and precise dimensions.
Shaping and Size Specification Standards
After molding, each piece undergoes shaping procedures to meet specified standards. These steps include trimming excess material and verifying dimensional conformity via sophisticated measuring tools.
Heat Treatment and Curing
Temperature Control in Kilns
Kilns are employed to subject the molded wheels to controlled heating cycles. Precise temperature regulation is pivotal in guaranteeing material stability.
Duration of Heat Treatment
The wheels remain in kilns for predetermined durations based on material composition and desired characteristics, optimizing hardness and tensile strength.
Effects of Curing on Wheel Strength and Performance
This curing stage solidifies the binder, anchoring abrasive grains firmly. Properly cured wheels exhibit improved robustness and retain honing efficacy over prolonged operational periods.
Precision Grinding and Surface Finishing
Grinding Processes for Correct Dimensioning
Further grinding processes hone the wheels to exact technical specifications, ensuring uniformity in thickness and diameter which aids balanced rotation during use.
Surface Finishing Techniques
- Lapping: Employs abrasive slurry to remove minor imperfections from the surface.
- Polishing: Enhances smoothness and reduces friction, adding a polished layer that endows optimal sharpness.
Ensuring Optimal Sharpness and Smoothness
These finishing steps culminate the manufacturing process, providing grind wheels ready to perform effectively upon implementation.
Quality Assurance and Testing
Testing for Mechanical Strength and Wear Resistance
Stringent testing protocols evaluate the wheels’ ability to withstand mechanical stress and reduce wear rates, assuring operators of reliable performance.
Balancing and Vibration Testing
Proper balancing tests eliminate undue vibrations during use, bolstering operator safety and prolonging machine life.
Ensuring Compliance with Industry Standards
Comprehensive QA checks certify compliance with international industrial norms, providing end-users with validated quality assurances.
Packaging and Distribution
Safe Packaging Methods to Prevent Damage
Protective packaging methodologies guard against transit-related damages, utilizing padded containers and secure sealing practices.
Labeling and Certification
Each package includes detailed labels displaying pertinent information along with certification stamps affirming authenticity and spec adherence.
Distribution Channels and Logistics
Streamlined logistics channels guarantee timely delivery, incorporating a network of trusted carriers and warehousing facilities to expedite order fulfillment.
Innovations and Future Trends
Advances in Abrasive Materials
Ongoing research catalyzes innovative developments in abrasive technology, leading to next-generation materials delivering even higher efficiencies.
Sustainable Manufacturing Practices
Adopting eco-friendly manufacturing processes aligns with global sustainability goals, reducing environmental impact while maintaining product excellence.
Future Market Trends and Demands
Anticipated market dynamics predict increased demand for customized grinding wheel solutions, focusing on tailored designs catering to diverse industrial needs.
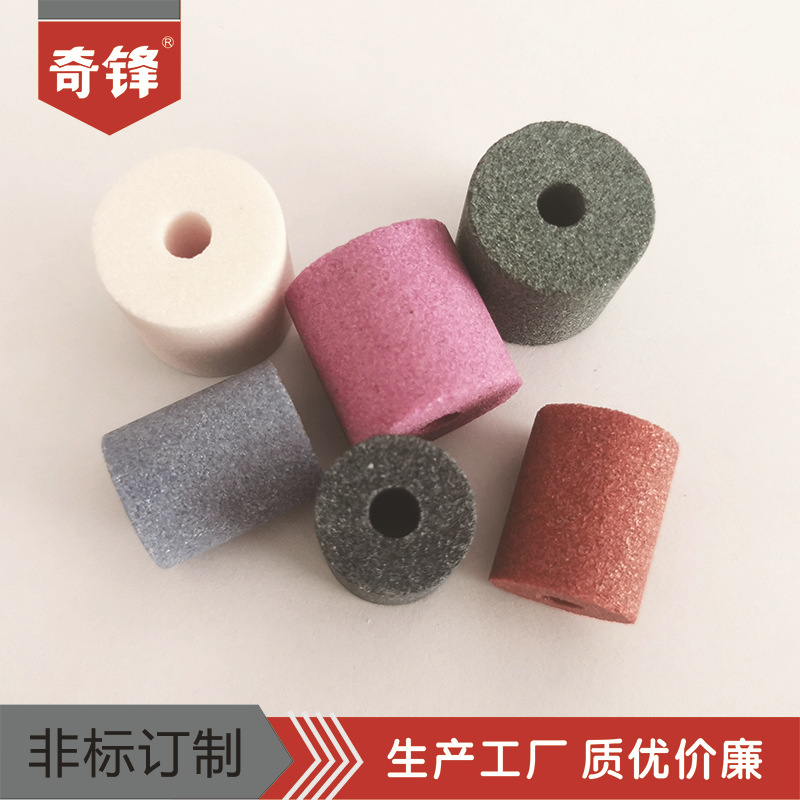